Poradnik, który aktualnie czytasz poświęcony będzie wadzie wypraski jakim jest niedolew. Analiza niedolewu pozwoli Ci zgłębić wiedzę na temat przyczyn powstawania oraz podpowie w jaki sposób przeciwdziałać jego wystąpieniu. Jakiś czas temu opublikowałem wpis na temat omawianej wady (kliknij), ale poniższy wpis będzie rozkładał problem na czynniki pierwsze. Wpis podzielony będzie na kilka części ponieważ jest zbyt długi na jeden post. W analizie skupie się na opisie wady, możliwych przyczynach powstawania błędu i ich rozwiązania. Przekazując ten poradnik do czytania liczę, że będzie on przydatny nie tylko ustawiaczom maszyn wtryskowych czy też technologom i inżynierom procesu. Mam ogromną nadzieję, że stanowił będzie doskonałe źródło wiedzy dla pracowników działów jakości, którzy często muszą odpowiadać na raporty 8D klientom.
Opis wady
Niedolew to część, która nie została całkowicie wypełniona tworzywem. Jest to zjawisko, w którym płynne tworzywo nie wypełnia całkowicie gniazda formującego. Taki niedolew najczęściej występuje na końcu drogi płynięcia, ale może powstać również na żebrach oraz na początku wtrysku. Krawędź w miejscu zakończenia płynięcia frontu tworzywa jest najczęściej zaokrąglona. Zaokrąglenie krawędzi wynika z przepływu laminarnego tworzywa w gnieździe formującym. Spójrz na Rysunek 1 – przedstawia on wypraskę z dolanymi obszarami oraz tą samą wypraskę z występującymi niedolewami. Niedolew w wypraskach może stanowić realne ryzyko utraty funkcjonalności części. Taka utrata funkcjonalności np. montażu lub zgrzania stanowi błąd krytyczny dla producenta i uniemożliwia wykorzystanie części przez klienta. Dlatego analiza niedolewu jest istotnym czynnikiem do permanentnego rozwiązania problemu.
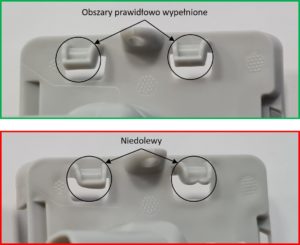
Analiza niedolewu – parametry procesu
W celu zbadania możliwych przyczyn musimy sobie wyznaczyć potencjalne źródła problemu. W tej części poradnika skupimy się na parametrach procesu. Kolejne części poświęcę pozostałym źródłom. Poddam wtedy analizie formę, maszynę i tworzywo – Rysunek 2.
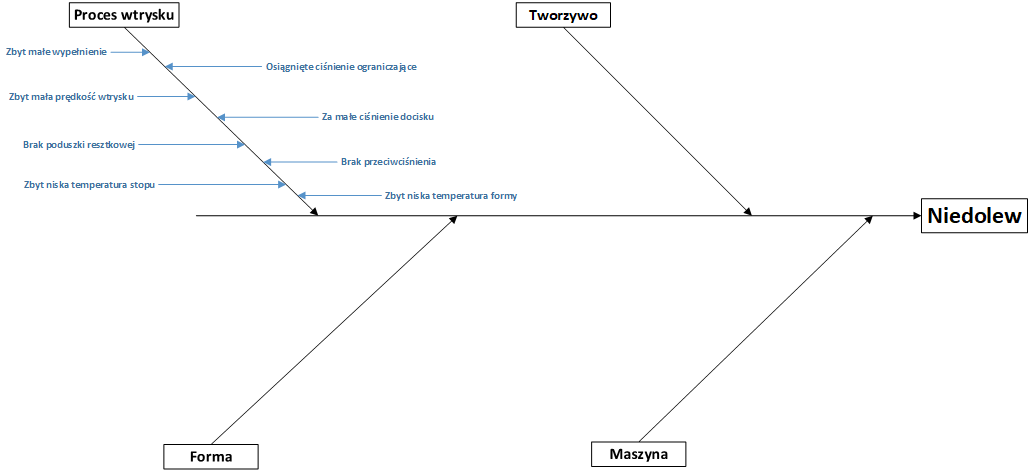
Potencjalne przyczyny występowania niedolewu związane z procesem wtrysku to:
- Zbyt małe wypełnienie.
- Osiągnięte ciśnienie ograniczające.
- Zbyt mała prędkość wtrysku.
- Za małe ciśnienie docisku.
- Brak poduszki resztkowej.
- Brak przeciwciśnienia.
- Zbyt niska temperatura stopu.
- Zbyt niska temperatura formy.
Ad. 1 – Zbyt małe wypełnienie
Zaleca się, żeby wypraska została wypełniona wtryskiem do 95-98% objętości. Jeżeli nie zastosujesz się do tej zasady to możesz mieć problem z powstawaniem niedolewu. Docisk nie zawsze jest w stanie uzupełnić tworzywem gniazdo formujące tym bardziej, jeżeli wypraska posiada cienkie żebra lub inne pocienienia. Jeżeli została zarejestrowana masa części bez docisku i umieszczona w dokumentacji procesowej to porównaj ją z aktualną wartością masy wypraski bez docisku. Jeżeli ciężar jest zbyt lekki, zbadaj potencjalne przyczyny, które mogą obejmować:
- Wielkość dozy jest zbyt mała.
- Punkt przełączenia został ustawiony zbyt wysoko.
- Występuje wyciek z dyszy.
- Zawór zwrotny jednostki plastyfikacji jest nieszczelny.
- Rozszczelnił się układ gorąco-kanałowy.
- Osiągnięty został czas ograniczający wtryskiwania.
Podczas ustalania wielkości dozy, ważne jest, żeby być pewnym, że tworzywo nie trafia w miejsce gdzie go nie powinno być. Istnieją przypadki, w których pracownik próbujący wyeliminować niedolew zwiększa drogę dozowania nie wiedząc, że materiał ten trafia do układu gorąco-kanałowego w wyniku jego rozszczelnienia, co powoduje jeszcze większe zalanie. Jeżeli nie zorientujemy się, po pierwszym lub drugim wtrysku może dojść do wycieku tworzywa z kanału kablowego od grzałek gorącego kanału. Jeżeli dysponujesz wiedzą na temat masy wypraski bez docisku z poprawnego procesu to porównaj ją z aktualną masą wypraski bez docisku. Dzięki temu będziesz w stanie zweryfikować czy stopień wypełnienia gniazda, czy nawet prędkość wtrysku nie uległy zmianom. Ma to kluczowe znaczenie dla zapewnienia powtarzalnego napełnienia formy wtryskowej.
Ad. 2 – Osiągnięte ciśnienie ograniczające
Wtryskarki umożliwiają ustawienie ograniczającego ciśnienia ograniczającego w celu ochrony formy przed ewentualnym przelaniem. Ciśnienie ograniczające powinniśmy ustawiać około 10% wyższe, niż ciśnienie wymagane do wtrysku akceptowalnej jakościowo części. Jeżeli ciśnienie ustawisz poniżej wymaganego do wtrysku, to zmniejszysz prędkość wtrysku powodując ryzyko wystąpienia niedolewu. Jeżeli ciśnienie ograniczające jest osiągane, może to być wynikiem:
- Zdolności maszyny. Maszyna może nie mieć wystarczającego ciśnienia.
- Zbyt nisko ustawionego ciśnienia ograniczającego. Upewnij się, że jest ustawione około 10% wyżej, niż wymagane do utrzymania zadanej prędkości wtrysku. Powyższa tolerancja zabezpieczy Twój proces wtrysku w przypadku zmian lepkości.
- Wtrącenia, które zmniejszy przekrój przepływu tworzywa. Dysza wtryskowa lub układ gorąco-kanałowy jest podatny na zatkanie jeżeli dostanie się tam np. kawałek metalu lub innego, stałego zanieczyszczenia. W przypadku stosowania filtrów w dyszach wtryskowych musisz być świadomy, że powodują one wzrost ciśnienia. Zanieczyszczenia, które będzie filtr wyłapywał będą to ciśnienie podwyższać.
- Niskiej temperatury dyszy lub gorącego kanału. W tym przypadku zwiększysz opory przepływu.
- Spadku ciśnienia na dyszy. Różnica średnicy tulei wtryskowej w odniesieniu do dyszy wtryskowej na maszynie nie powinna być zbyt duża, gdyż będzie to miało wpływ na spadek ciśnienia. Więcej na ten temat przeczytasz we wpisie dotyczącym średnicy dyszy wtryskowej.
Jeżeli proces wtrysku będzie ograniczony ciśnieniem, to prędkość wtrysku będzie się zmniejszała. Dla lepszego zrozumienia tego procesu zwróć uwagę na Rysunek 3, który przedstawia proces z prawidłowo ustawionym ciśnieniem ograniczającym oraz proces z ciśnieniem ograniczającym ustawionym zbyt nisko. Prędkość wtrysku jest w tym przypadku zmniejszana przez ograniczenie ciśnienia co może być powodem powstawania niedolewów.
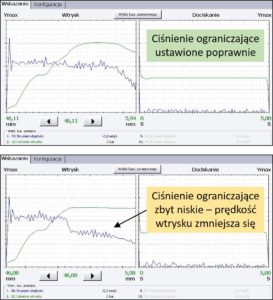
Weryfikację przyczyny spadku ciśnienia możesz wykonać za pomocą częściowego wypełniania gniazda i rejestrowaniu przy tym maksymalnych ciśnień dla różnych faz wypełniania. W ten sposób ustalisz obszar, w którym spadek jest największy i będziesz w stanie podjąć dalsze kroki.
Ad. 3 – Zbyt mała prędkość wtrysku
Jeżeli prędkość wtrysku zaprogramujesz zbyt wolno, to nie wypełnisz całkowicie gniazda formującego. Szybki wtrysk jest w większości przypadków pożądany, ponieważ szybkie prędkości wypełniania pomagają utrzymać stałą lepkość tworzywa i ograniczają spadki ciśnienia na drodze wypełniania.
Porównaj czas wtrysku z dokumentacji procesowej z aktualnym czasem wypełniania. Jeżeli aktualny czas wtrysku jest dłuższy, zweryfikuj czy zaprogramowana prędkość jest prawidłowa i ewentualnie dokonaj jej zwiększenia. Zwróć przy tym uwagę, czy maszyna osiąga zadane prędkości. Do tego celu możesz użyć wykresów rejestrujących rzeczywistą prędkość wtryskiwania w maszynie i porównać ją z parametrami zadanymi, co możesz zaobserwować na Rysunek 4. Jeżeli maszyna nie realizuje zadanych prędkości zgłoś to swojemu działowi utrzymania ruchu lub bezpośrednio do działu serwisowego producenta/dostawcy wtryskarki. Czas wtrysku i masa wypraski bez docisku są ważnymi miarami, które powinieneś umieszczać w dokumentacji procesowej. Wartości zadane, które programujemy na maszynie nie powinny stanowić podstawy do oceny procesu wtrysku, ponieważ niektóre maszyny używają procentowej wartości prędkości wtrysku, co nie będzie miarodajne. Zawsze polegaj na masie wypraski i czasie wtryskiwania.
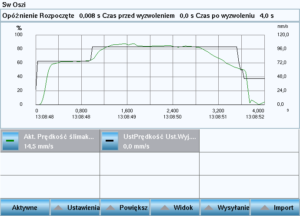
Kolejnym miejscem występowania niedolewów mogą być żebra w pobliżu punktu wtrysku. W wyniku dużej prędkości wtryskiwania, czoło płynącego stopu przepływa po najmniejszej linii oporu, a żebro może zostać dolane dopiero po osiągnięciu podwyższonego ciśnienia w gnieździe formującym. To stanowi duże ryzyko powstawania omawianej wady, przede wszystkim dla żeber umieszczonych poprzecznie do kierunku przepływu tworzywa. W takich przypadkach zmniejszenie prędkości wypełniania może pozytywnie wpłynąć na eliminację niedolewu. Należy przy tym dokonać kontroli, czy żebro jest prawidłowo odpowietrzane.
Ad. 4 – Za małe ciśnienie docisku
Jeżeli ustawisz ciśnienie docisku zbyt małe, to możesz doprowadzić do powstania niedolewu. Po wypełnieniu gniazda formującego do 95-98% objętości powinniśmy przejść ze sterowania prędkością na sterowanie ciśnieniem w wyniku działania docisku. Pod wpływem docisku, gniazdo formujące uzupełni pozostałe 2-5% objętości oraz straty skurczowe w wyprasce. Cienkie żebra i podobne wrażliwe na wadę miejsca na wyprasce wymagają wystarczająco dużego ciśnienia, żeby wcisnąć tworzywo w zagłębienia w formie. Jeżeli ciśnienie docisku będzie za małe powstanie niedolew.
Ad. 5 – Brak poduszki resztkowej
Poduszka resztkowa będąca parametrem wynikowym to bufor pomiędzy głowicą wtryskarki, a końcówką ślimaka. Bufor ten stanowi pewną ilość tworzywa, która pozostaje przed końcówką ślimaka po zakończeniu trwania procesu docisku. Zadaniem poduszki resztkowej jest przeniesienie ciśnienia stopu do gniazda formującego, celem uzupełnienia strat skurczowych powstających w wyprasce. Jeśli poduszka resztkowa osiąga zero, oznacza to, że doza jest zbyt mała lub nastąpił wyciek materiału. Ewentualnym źródłem wycieku/przecieku może być:
- Zawór zwrotny ślimaka.
- Dysza zamykana na maszynie.
- Miejsce styku tulei z dyszą wtryskową.
- Wyciek z układu gorąco-kanałowego.
- Wyciek z podziału formy.
Dokonaj weryfikacji powyższych punktów celem ustalenia źródła problemu.
Jeżeli na maszynie nie pozostaje poduszka resztkowa i nie ma wycieku tworzywa, to należy ponownie ustalić drogę dozowania i punkt przełączenia na docisk. Bardzo dobrą praktyką jest nadzorowanie wielkości poduszki resztkowej poprzez dostępne na maszynie opcje. Monitorowanie wartości poduszki pozwala zatrzymać produkcję w przypadku przekroczenia zastosowanych tolerancji.
Ad. 6 – Brak przeciwciśnienia
Problem z przeciwciśnieniem może się rozpocząć podczas przetryskiwania agregatu. Często w wyniku powstającego ciśnienia w układzie plastyfikacji następuje wyciek materiału z dyszy wtryskowej podczas dozowania. W takim przypadku technik redukuje przeciwciśnienie w celu zadozowania tworzywa, co może skutkować powstawaniem niedolewów w wyniku zmniejszenia gęstości stopu. Podczas ponownego rozruchu należy przywrócić wartości do poprawnych.
Ad. 7 – Zbyt niska temperatura stopu
Niska temperatura stopu zwiększa lepkość tworzywa, co powoduje, że materiał płynie gorzej. Tworzywo o wysokiej gęstości nie będzie w stanie wypełnić niektórych miejsc wypraski i będzie powodowało spadek ciśnienia na drodze wypełniania doprowadzając do powstania niedolewu. Dokonaj kontroli temperatury stopu za pomocą odpowiedniego czujnika i porównaj z dokumentacją procesową i kartą techniczną tworzywa. Zwiększenie temperatury formy to często stosowany zabieg w celu poprawy wypełnienia formy. Zwiększenie tej temperatury może wymuszać wydłużenie czasu chłodzenia lub doprowadzić do degradacji materiału.
Ad. 8 – Zbyt niska temperatura formy
Prawdopodobnie zastanawiasz się dlaczego mówimy w tej części o formie. Już wyjaśniam, ponieważ temperatura formy to parametr procesowy.
Niskie temperatury formy mogą wpływać na skuteczność wypełnienia gniazda formującego tworzywem. Niska temperatura formy skutecznie odbiera ciepło z płynnego materiału powodując zwiększenie zakrzepniętej warstwy tworzywa, co ogranicza przepływ w formie. Forma w wyniku przepływu gorącego stopu podnosi swoją temperaturę. Jeżeli wypraska posiada trudne do wypełnienia obszary to początkowe wtryski mogą posiadać wady w postaci niedolewu wynikające z niskiej temperatury powierzchni narzędzia. Dobrą praktyką jest zarejestrowanie temperatury powierzchni formującej i wypraski podczas wyformowania z zastosowaniem ręcznej termopary i kamery termowizyjnej oraz umieszczenie tych danych w dokumentacji procesowej. Nastawy na regulatorach temperatury nie wskazują rzeczywistej temperatury pracy formy. Temperatury te cechują wahania, które wynikają z odbioru ciepła ze stopu i oddawania go do układu chłodzenia formy wtryskowej (Rysunek 5).
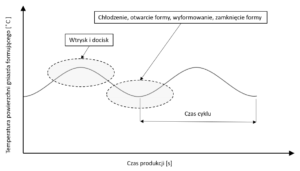
Podsumowując
Przede wszystkim dziękuję Ci za wytrwanie do końca tego wpisu 🙂 Mam nadzieję, że opisana przeze mnie analiza niedolewu związana z parametrami procesu pozwoli Ci uniknąć tej wady. Jak widzisz, jest to jedynie część przyczyn. Proces wtrysku jest bardzo skomplikowanym etapem produkcji, zależnym od wielu czynników. Jako ustawiacze maszyn wtryskowych musimy mieć świadomość w jaki sposób możemy się przyczynić do wystąpienia wady. Dzięki temu będziemy w stanie ograniczyć brakowość na hali i tym samym zabezpieczyć klienta przed wadliwymi sztukami, a naszą firmę przed reklamacją. Dlaczego to jest tak ważne? Ponieważ w ten sposób zabezpieczasz sam siebie przed zakupem wadliwego wyrobu 😊
Pingback: Analiza niedolewu - forma - Ascons . Poradnik Ustawiacza Wtryskarek
Pingback: Analiza niedolewu – forma – WordPress