Zużycie energii jest problemem na całym świecie, które dotyka również branżę przetwórstwa tworzyw sztucznych, więc włącz oszczędzanie to nie tylko slogan. Ze względu na rozwijające się coraz bardziej restrykcyjne przepisy dotyczące efektywności energetycznej, inwestowanie w tym obszarze stwarza duże możliwości dla przemysłu. Przykładowy udział faz procesu wytwarzania na całkowite zużycie energii przedstawia Rysunek 1. Obniżenie kosztów, zwiększenie produktywności i zmniejszenie wpływu na środowisko to tylko kilka przykładowych profitów.
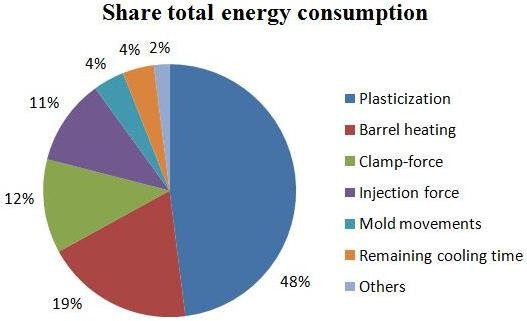
Projektuj optymalnie
Części projektowane pod proces wtryskiwania mają odpowiednie zalecenia dotyczące ich konstrukcji. Stosowanie tych zaleceń, poza poprawą jakości części, ma również wpływ na zużycie energii elektrycznej podczas produkcji.
Różne rodzaje tworzyw mają różne zalecenia w zakresie długości przepływu w stosunku do grubości ścianki. Zrozumienie zachowania się tworzywa podczas przepływu dostarcza bezcennych informacji, które mają bezpośredni wpływ na koszty produkcji (Rysunek 2).
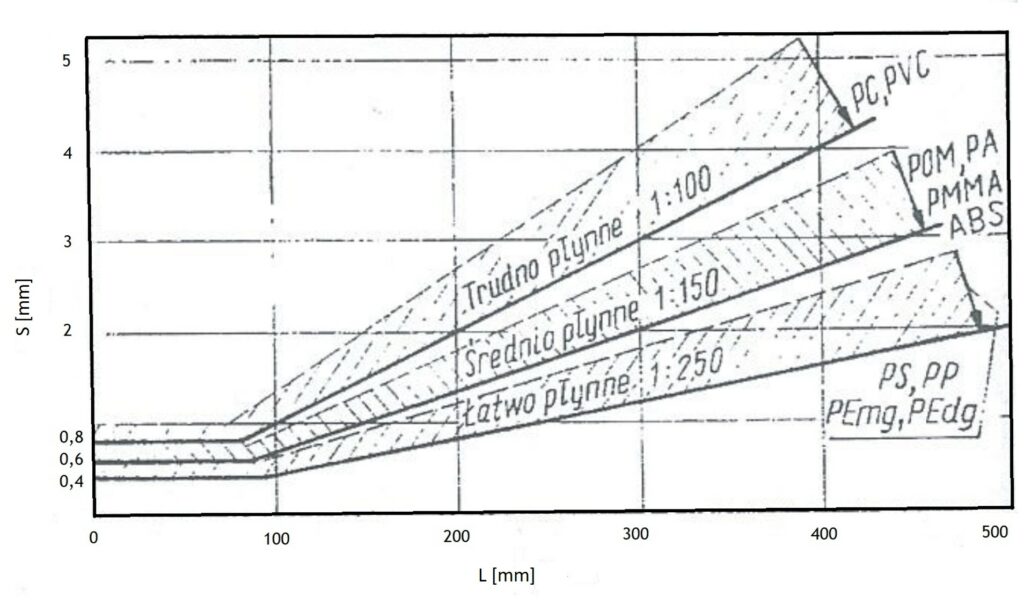
Grubość żebra u podstawy i jego wysokość to kolejny obszar projektu wypraski, dzięki któremu możemy zaoszczędzić energię podczas produkcji. Grube żebro wymaga dużych ciśnień, żeby nie wystąpiła wada, którą nazywamy wciągiem. Stosunek grubości żebra do podstawowej grubości ścianki powinien mieścić się w zakresie 40-60%. Natomiast wysokość żebra powinna być < 4x grubości ścianki (Rysunek 3).
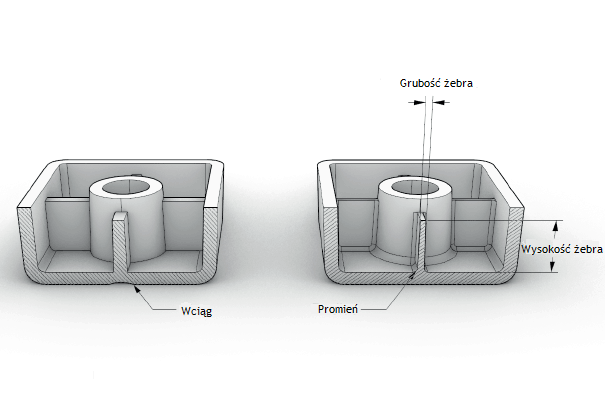
Taki projekt wypraski daje możliwość uzyskania szerokiego okna procesowego, zapewnia niskie straty ciśnienia, co bezpośrednio wpływa na optymalną produkcję elementów wtryskiwanych.
Kontroluj suszenie tworzywa
Niektóre tworzywa termoplastyczne należą do grypy materiałów higroskopijnych (np. PA, PC, PET) co wymusza ich suszenie przed wykorzystaniem do produkcji. Faza suszenia tworzywa zużywa nawet 15% całkowitej energii zużywanej do przetwórstwa tworzyw sztucznych. Odpowiednie wykorzystanie suszarek i ich optymalne ustawienie może przynieść duże oszczędności energii. Punkt rosy suszarki ze złożem molekularnym powinien mieścić się w zakresie -25°C do -50°C. Im bliżej -50°C będzie ustawiony tym większe będzie zużycie energii, które nie spowoduje istotnego przyspieszenia suszenia.
Jeżeli istnieje możliwość zastosowania tworzywa niechłonącego wilgoci bez wpływu na właściwości wypraski to warto przemyśleć ten krok. Wybór niehigroskopijnych tworzyw sztucznych, tam gdzie jest to możliwe, przyczyni się do znaczących oszczędności w zużyciu energii elektrycznej.
Utrzymuj temperaturę formy ograniczając straty ciepła
Wykorzystanie do produkcji technicznego tworzywa (np. PA, POM) wymaga stosowania wysokich temperatur formy, nawet powyżej 100°C. Forma, która jest zamocowana na wtryskarce styka się z płytą maszyny całą powierzchnią mocującą. Tak duża powierzchnia styku powoduje istotny przepływ ciepła z formy do konstrukcji maszyny. Odbiór ciepła przez maszynę wpływa na pracę termostatu, który w takim przypadku będzie zużywał większą ilość energii w celu zapewnienia stabilnej temperatury formy.
Dobrą praktyką w opisanym powyżej przypadku jest stosowanie płyt izolacyjnych na formach wtryskowych, które zdecydowanie zminimalizują proces przepływu ciepła do konstrukcji maszyny (Rysunek 4).
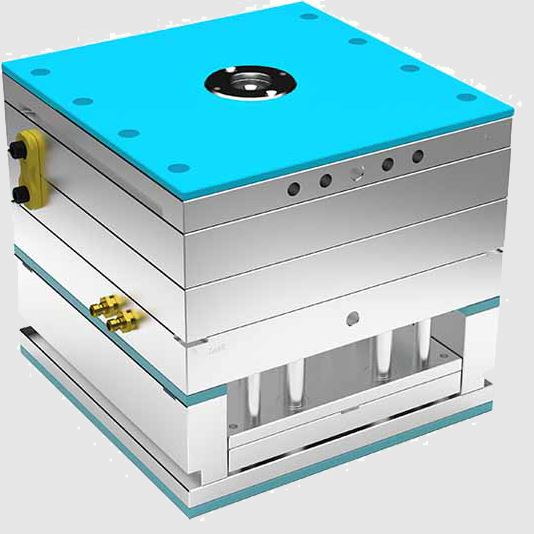
Ogranicz starty ciepła na cylindrze wtryskowym
Maszyna wtryskowa wymaga dużej ilości energii do pracy. Rozgrzanie i utrzymanie temperatury cylindra wtryskowego pochłania jej znaczącą ilość. Maty termoizolacyjne pozwalają w znaczny sposób zniwelować występujące straty energii cieplnej (Rysunek 5). Zastosowanie mat termoizolacyjnych zmniejsza ilość energii elektrycznej używanej do ogrzania cylindrów wtryskarki nawet o 40% (Rysunek 6). Pieniądze zainwestowane w zakup mat termoizolacyjnych zwracają się już po kilku miesiącach.
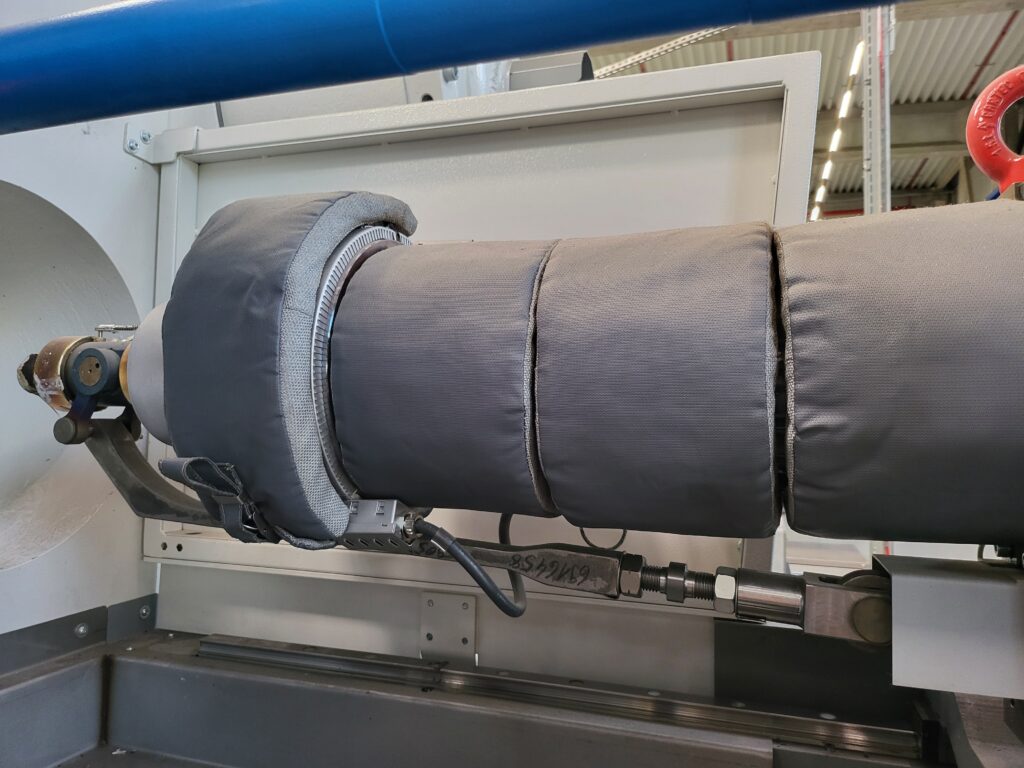
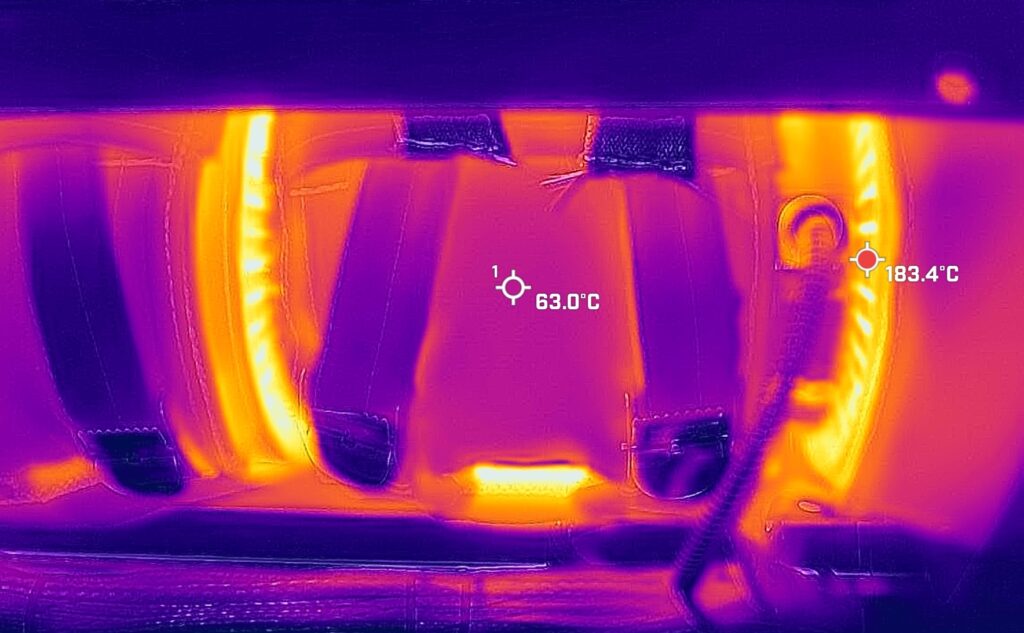
Maty termoizolacyjne polecane są przede wszystkim tam, gdzie mamy mono produkcję lub ewentualne zmiany tworzywa nie wymuszają dużych zmian temperatury cylindra. Związane jest to z długim oczekiwaniem na wychłodzenie cylindra np. przy zmianie tworzywa z PA6.6 na PE (czyli obniżenie z temperatury ~290°C do temperatury ~210°C). Czas oczekiwania na zmniejszenie temperatury ma w takim przypadku bezpośredni wpływ na wydłużenie czasu przezbrojenia.
Inwestuj w ludzi
Efektywność energetyczna to nie tylko projekt wypraski czy sprzęt wykorzystywany do produkcji. Istotną rolę odgrywa także sposób funkcjonowania wtryskowni. Szkol swoich pracowników poprzez szkolenia wewnętrzne oraz zewnętrzne, które będą podnosić świadomość i przyczyniać się do oszczędności energii.
Kluczowe czynniki, o które powinien zadbać pracownik to m.in. reakcja na wszelkiego rodzaju wycieki tj. sprężonego powietrza, wody, oleju. Każdy taki ubytek medium wpływa na bezpieczeństwo pracy i zużycie energii. Ich szybka eliminacja pozwala podnieść efektywność funkcjonowania zakładu produkcyjnego.
Optymalnie ustawiony proces wtrysku to podstawa w każdej wtryskowni. Korzystając ze szkoleń z zakresu ustawiania parametrów wtrysku masz możliwość podniesienia kwalifikacji pracownika i przyczynienia się do zmniejszenia strat. Tego typu inwestycja podnosi również morale, które mają bezpośredni wpływ na zaangażowanie w pracy.
Podsumowanie
Włączenie oszczędzania to nie moda, to konieczność która umożliwi dalsze funkcjonowanie i rozwój firm z branży przetwórstwa tworzyw sztucznych.
Kilka przykładów przytoczonych w tym artykule, które mogą zwiększyć efektywność energetyczną wtryskowni zdecydowanie nie wyczerpuje wszystkich dostępnych opcji. Wdrażaj zmiany małymi, zdecydowanymi krokami – zacznij produkować efektywniej.