Warunki formowania w przetwórstwie tworzyw sztucznych metodą wtryskiwania mają znaczący wpływ na końcowe właściwości tworzywa, niezależnie od konstrukcji wypraski. Temperatura formy w procesie wtrysku to kolejny kluczowy parametr, któremu się bliżej przyjrzymy. Wcześniej zachęcam do zapoznania się z ostatnio opisaną przeze mnie temperaturą układu plastyfikacji 🙂
Ważne jest, żeby ustawiacz odróżniał parametry nastawcze w prowadzonym procesie od parametrów wynikowych. Temperatura powierzchni formującej może być zbliżona do temperatury medium chłodzącego, ale niekoniecznie taka sama.
Układ regulacji temperatury formy to jeden z czynników odpowiedzialnych za jakość produkowanych wyprasek. Jego celem jest odprowadzenie ciepła dostarczonego wraz z wtryskiem przy zachowaniu równomiernego rozkładu temperatur na powierzchniach formujących.
Regulując temperaturę formy spotykamy się z przeciwstawnymi wymaganiami i musimy dokonać pewnego kompromisu pomiędzy:
- uzyskaniem optymalnej jakości wypraski, której właściwości kształtują się przy podwyższonej temperaturze formy i równomiernym rozkładzie obioru tego ciepła,
- rentownością prowadzonej produkcji zależnej od rzeczywistego czasu cyklu, na który ma wpływ stosowanie niskich temperatur formy.
Przy produkcji wyrobów powszechnego użytku (np. opakowań itp.) często stosuje się intensywny odbiór ciepła, jeżeli chce się być konkurencyjnym na rynku. Dla wyrobów technicznych istotne są parametry m.in. wytrzymałościowe oraz względy wizualne, które osiągniemy stosując podwyższone temperatury powierzchni formujących.
W polimerach amorficznych (np. PC, ABS) wyższe temperatury formy powodują niższy poziom naprężeń. Dla tworzyw częściowo krystalicznych (np. PA, POM) uzyskanie optymalnej krystalizacji osiąga się poprzez stosowanie wyższych temperatur formy. W ten sposób zapewniamy wolniejszy odbiór ciepła i dajemy czas na wytworzenie się krystalitów, które zapewniają lepsze właściwości mechaniczne i lepszą stabilność wymiarową.
Wymienione korzyści nie są jedynymi w kontekście podwyższonej temperatury formy. Dzięki termostatowaniu narzędzi do optymalnych wartości uzyskujemy również:
- poprawę płynięcia tworzywa w gnieździe formującym,
- lepszą relaksację makrocząsteczek w wyniku zmniejszonej orientacji,
- możliwość efektywniejszego działania procesu docisku.
Szeregowo podłączony układ chłodzenia
W metodzie szeregowego podłączenia układu chłodzenia przez formę prowadzi tylko jeden kanał z wejściem i wyjściem dla medium chłodzącego. Taki sposób podłączenia pozwala na użycie tylko jednego obiegu dostępnego na maszynie lub tylko jednego termostatu, co znacznie upraszcza podłączanie. Wadą takiego rozwiązania jest wzrost temperatury wraz z przebiegiem kanału chłodzącego. W związku z tym różne obszary powierzchni formującej mogą mieć różną temperaturę, co nie zapewnia równomiernego odbioru ciepła i może być przyczyną odkształceń wypraski (Rysunek 1).
Równolegle podłączony układ chłodzenia
W przypadku podłączenia równoległego zasilanie obiegów chłodzących na formie odbywa się przy pomocy rozdzielacza. Dzięki temu jesteśmy w stanie równomiernie odbierać ciepło z powierzchni formujących. W przypadku zablokowania się jednego z kanałów chłodzących istnieje ryzyko braku odbioru ciepła z chłodzonego obszaru. Taka sytuacja w podłączeniu równoległym jest bardzo trudna do wykrycia (Rysunek 1).
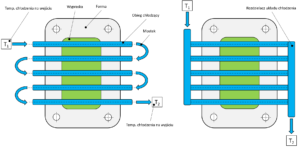
Weryfikacja temperatury formy wtryskowej
Weryfikacja temperatury formy powinna się odbyć po kilkunastu minutach produkcji w cyklu automatycznym. W ten sposób forma wtryskowa stabilizuje swoją temperaturę, która zależy m.in. od temperatury wtryskiwanego stopu, temperatury medium chłodzącego, konstrukcji układu chłodzącego w formie, sposobu podłączenia tj. czy szeregowo czy równolegle, czasu cyklu itp.
Urządzeniem kontrolnym może być np. termopara powierzchniowa (Rysunek 2), dzięki której odczytamy rzeczywistą temperaturę w badanym obszarze. Pomiar stykowy jest dobrym sposobem weryfikacji czy nie dochodzi do przegrzania konkretnego obszaru, w którym np. wypacza się wypraska.
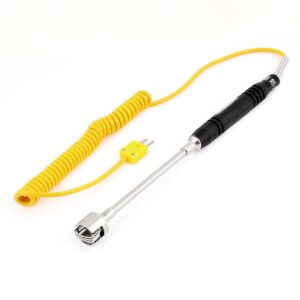
Kolejną metodą służącą ocenie skutecznego odbioru ciepła jest pomiar różnicy temperatury na wyjściu z termostatu oraz na jego powrocie po odbiorze ciepła z formy wtryskowej. W tym celu można zastosować termometr przepływowy lub wykonać zdjęcie kamerą termowizyjną w celu określenia temperatury. Przykład takiej kontroli obrazuje Rysunek 3 oraz Rysunek 4. Termogramy przedstawiają przewody zasilające układ chłodzenia formy wtryskowej oraz przewody powrotne. Różnica temperatury pomiędzy zasilaniem i powrotem nie powinna być większa niż 3°C. Jeżeli jest wyższa to istnieje ryzyko nierównomiernego odbioru ciepła z wypraski i tym samym jej wypaczania.
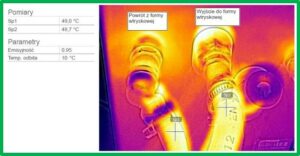
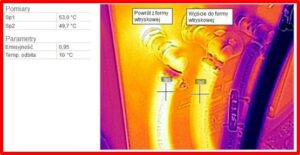
Podsumowanie
Zapewnienie skutecznego i równomiernego odbioru ciepła z formy wtryskowej to jeden z najważniejszych aspektów w procesie wtryskiwania. Jakość wyprasek i koszt ich wytworzenia w dużym stopniu uzależnione są od prawidłowego działania systemu chłodzenia. Temperatura formy w procesie wtrysku to już drugi artykuł, który został umieszczony w czasopiśmie branżowym PlastNews. Poniżej załączam dla Was wersję w .pdf.
POBIERZ .PDF – Temperatura formy wtryskowej w procesie wtrysku
Pingback: Prędkość wtrysku - ASCONS